SSIA
Semiconductor initiatives in Arizona with ASU and NXP
Dr. Zachary Holman, Associate Prof., School of Electrical, Computer, and Energy Engineering, and Director of Faculty Entrepreneurship, Arizona State University, USA, spoke about the semiconductor initiatives taken on by Ira A. Fulton Schools of Engineering, ASU, on day 3 of the Semiconductor Business Connect 2021 organized by the SSIA.

Dr. Holman said ASU builds engineers and innovators. There over 127,500 master learners across five campuses. 25,000 students at the Ira A. Fulton Schools of Engineering 218 national merit scholars, 232 national hispanic scholars, one-third of the Honors College. Fulton Schools faculty has received over 32 national science foundation awards over the last three years. There are 50+ graduate degree programs. There was over $127 million in research expenditures in FY 2019-20.
There are seven different schools at Ira S. Fulton Schools of Engineering, ASU. These are: School of Computing and Augmented Intelligence, The Poly School, School of Electrical, Computer, and Energy Engineering, School of Manufacturing Systems and Networks, School of Sustainable Enginnering and Built Environment, and School of Health Systems Engineering. They produce a lot of graduates. An ASU student team’s fog-free mask design won $1 million in an international competition. Another team won $340,000 in cash and services at the 5th annual pitch competition. The new entrepreneurship master’s degree combines design, business and engineering. ASU will lead the effort to upskill and reskill workforce through $8 million grant by the US Department of Labour.
ASU MTW
ASU MacroTechnology Works (MTW) is a world-class semiconductor facility. Located in Tempe, Arizona, it has 250,000 sq. ft. total capacity and 43,500 sq. ft. of cleanroom space. MTW is a research ecosystem. Its mission to be the engine of semiconductor and energy research in the USA. It is a national resource for getting new technology to pilot scale. Key capability areas have been power electronic displays, solar batteries, etc. MTW and tools are larger than university cleanroom or nanofab facilities. Core facility toolsets include advanced electronics and photonics (AEP) 150mm tools, AEP Gen II tools, and solar power lab (SPL) M2 tools.
At ASU, work is being done by corporate partners, such as Applied Materials, Cactus Materials, Swiftcoat, Advent, AmberWave, Sunflex Solar, Von Ardenne, EVG, Applied Microarrays, 2D Semiconductors, etc. The work done is across solar, semiconductors, materials, and batteries. You can join the MTW ecosystem and get access to equipment, faculty/research expertise, and pipeline of trained students. MTW can work for you, by using core faculty while onsite, leasing space onsite, and accessing core facility from afar.
Growth plans include new materials, power electronics, and advanced packaging. For new materials, there are plasma etch and deposition processes, new precusor chemistries, and advanced characterization. For power electronics, there are wide-bandgap materials, such as SiC, GaN, GaO, and diamond, high frequency and high power, and circuits with power electronics. For advanced packaging, there are chip stacking and 3D integration, integration of heterogenous materials and devices, and metallization.
NXP and Arizona
Geno Fallico, VP of Operations, Chandler Fab, NXP Semiconductors Inc., presented the closing note about what it is doing in Arizona, USA. Motorola had set up shop here, back in 1949. Their success attracted a lot of other companies.

As the semiconductor ecosystem grew in Arizona, there were some spin-offs. We became Freescale, the semiconductor division. It later merged with NXP, which has six fabs across the world. We have SSMC fab in Singapore, two in Austin, Texas, one in the Netherlands, and two in Chandler, Arizona. Using GaN on SiC means, we have a 6-inch fab in Chandler.
We have had the headquarter here for a long time, along with the university. Arizona has a stable power grid. Austin sites are not as lucky. Locally, we have a good talent pool. Nationally, it was easy to hire people. We have done projects with the university teams. Phoenix Airport is about 15 minutes from our site.
Fast forward to the rapid market recovery, we have to rapidly get back to 2019 levels. We have been aggressively ramping and adding equipment. We have good success in getting new people. We have identified training. USA and Arizona have awarded grant to ASU. Arizona has strategic water supply and power grid. We are continuing to grow. Arizona is also supporting the semiconductor industry.
Automated smart FDC and ML at edge in fabs
James Bramante, Data Scientist, Inficon, presented on automated FDC: ML at the edge, on day 2 of the ongoing Semiconductor Business Connect 2021 organized by Singapore Semiconductor Industry Association (SSIA).

ML in the fab requires innovative infrastructure. Fault detection and classification (FDC) can be made smarter via automation of anomaly detection and deployment of advanced models on the edge. Inficon supplies sensors and software to fabs worldwide. Inficon has two intelligent manufacturing systems. The final phase systems decides when, how, and where to move wafers to improve productivity. FabGuard monitors process equipment health to prevent wafer scrap. We have engineering-focused FDC.
Inficon Smart FDC leads to less material and time wastage. Automation can increase labor productivity, reduced waste material and time in the fab. It also reduces opportunities for human error. Inficon decided on a hybrid ML and engineering approach. ML can make FDC smarter. It uses AI and ML. ML can be trained for a very specific task with clean data and well-defined domain boundaries. You can also pre-process, transform, or summarize data to inform or facilitate a human decision maker. SmartFDC uses ML to assist with decision-making process. Productivity requires interpretability and feedback.
There are models at the edge. There is edge computing and deployment for ML. In the common central server/cloud computing paradigm, all data is transferred to a central server for processing. Models are applied, and instructions and data are transferred back to the tools. Edge computing moves data processing and decision making closer to the edge nodes. Edge nodes are IoT devices or servers on LAN.
Edge computing increases the complexity of the setup and model maintenance. There are improvements to fab efficiency, and fab integration is also complex. Models at the edge automates model deployment across entire fabs.
Semiconductor underpins industry growth
Semiconductor Business Connect 2021 concluded with a panel discussion. The participants were Dr. Hai Wang, Intel, Tan Yew Kong, GlobalFoundries, and Ms. Jamie Neo, HP.
Opening the discussion, Dr. Wang said we had exercised stress on the supply chain. We are now getting better. More capacity is getting added. There is capacity stress on substrates, etc. Demand and supply was grossly mismatched. It will take some time to rectify.
Yew Kong said the sudden need for chips caught everyone by surprise. We are trying to add capacities. You have to try your best to support as many customers. They have also been accommodative. We are trying to put as many materials into the line. We cannot afford to have long downtime in the factory.
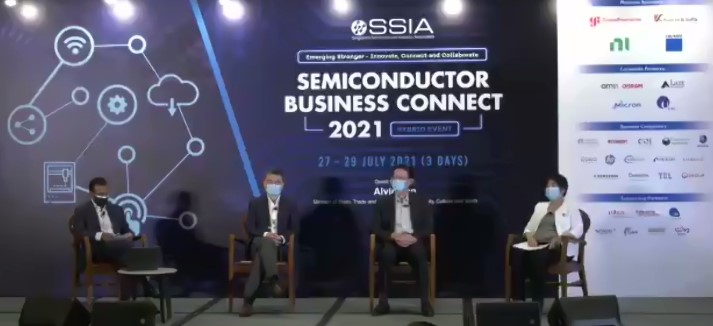
Ms. Neo said the global pandemic has been tough. Demand for our printers has been huge. We fared better in the areas where we applied Industry 4.0. This should also be accelerating our efforts.
Yew Kong added there was lot of assessment of the situation. This is a structural change. Acceleration of digital transformation will always be there. You will need even more chips going forward. We are going to be more dependent on chips in the future. In the coming decade, the semiconductor industry can grow to over $1 trillion. We have never stopped innovating. The mismatch can last for a few more months.
Capturing opportunity
Regarding Singapore capturing the opportunity, the vision is to double up the manufacturing sector. Semiconductor underpins industry growth across many areas. It is going to be promising. We need to support the ecosystem.
Dr. Wang said there is an area for talent. We don’t have enough talent yet, to grow. Singapore is looking to have more engineers. We need to encourage more Singaporeans to study engineering. It is related to core IP. Singapore also needs to think about how they are positioning the country in terms of an IP-rich arena. We have this decoupling trend in semiconductors. Singapore should upgrade to take advantage of the IP portfolio.
Ms. Neo added that we need to get into the ecosystem. We need to work with suppliers and end manufacturers. We are working on advanced manufacturing. Tapping into universities and polytechnics is also required. We have made some strides in data analytics. We can also work in collaboration projects. There are lots of opportunities for talent and collaboration.
Dr. Wang said Singapore should be looking to build on its advantages. It should focus on building on regional supply chain, and the global supply chain. Talent is an issue. The industry needs technology leadership talent. Very few companies have VP-level executives in Singapore. That needs to change.
Ms. Neo agreed, stating developing talent is very important. We need to tap into professional programs. We need to build on the domain knowledge and build upskilling. We are working on RPA. We need to create citizen developers.
Yew Kong added that talent is not that easy to develop within Singapore. We need to learn to be more productive. It is still very challenging for Singapore to be fully dependant. We are trying to reduce stress. Now, people are less keen on taking up technical jobs. We also need to train leaders. We can help to bring up leaders.
Dr. Wang said automation is driven by costs. It can drive demand for engineers up. Singapore needs to upgrade its labour force. We can encourage them to study engineering. AI can liberate people. He encouraged people to study engineering.
How does putting a factory in Malaysia help with Singapore’s GDP? Dr. Wang said we were trying to establish an RF team in Singapore. We could not to it. We need to focus on what we are good at, and team up with others to form a regional supply chain.
Dr. Wang said that semiconductor apps are growing. In the microscopic level, some cyclical forces are seen. We may see slight overcapacity in some of the categories. However, it will be pretty shallow. He said demand will increase for engineering jobs. Yew Kong added that Singapore needs stronger collaborations. We need to develop talent, and promote the industry.
Semicon supply chain reconfiguration and strengthening local ecosystem
There was a session on supply chain reconfiguration in the new normal at the ongoing Semiconductor Business Connect 2021.

Dr. Hai Wang, Corporate VP, GM, Product Supply Chain and External Manufacturing, Intel, said cloud, connectivity, AI, and intelligent edge are powering digital disruption. Semiconductor industry has been growing. We expect strong industry growth. IoT and automotive have high growth CAGR. and phone and PCs/servers continue to lead. Increasing functionality also increases the complexity. Today, disaggregation/modularity introduces more flexibility and capacity, but further complicates the supply chain. Modular supply chain requires to end data visibility and connections.
The number of countries participating in semiconductor manufacturing is very significant. For instance, 27 countries are involved in chip design. Increasing lead times require higher levels of co-ordination across the supply chain. Lead time almost doubled over the last decade. We are seeing many weak points in the supply chain. A $0.20 part can idle an automotive factory. We are sometimes at the mercy of specialized chemicals, photomasks, tools manufacturers, and SOI wafers.
We have some changing priorities. There is weakening global resilience and more costly supply/operations. From just-in-time, we have moved to just-in-case. Delays make things costly. There are higher sustainability expectations. We are also having decreasing flexibility. We are also using antiquated IT systems. We need to focus on security and risk management, and also efficiency. Strategic SCM becomes very important. There is reversing trend in pricing. Besides security, risk and efficiency, we also need to focus on agility, visibility and redundancy.

Strengthening local ecosystem
Tan Yew Kong, VP And GM, Fab Management, GlobalFoundries, talked about the strengthening the local ecosystem. We have seen a decade happening in a year, thanks to the pandemic. Technology is now enabling a better normal. 5G super cycle is here. Global trade is creating tailwinds. We are having accelerated global demand. The wafer fab operation during pandemic has been interesting. Maintaining operational KPIs in advanced 300mm fabs is important. We are seeing moderate impact on manual operations in 200mm fabs. There is Industry 4.0 acceleration across the world.
We are seeing material supply issues, as well as those in shipping and logistics. There have been struggles in the local service ecosystem. The local ecosystem makes a difference to supply resilience. We faced challenges on facilities services support. There was heavy reliance on foreign labor resources. More adoption on innovative automation and Industry 4.0 is going on. We need to strengthen the local ecosystem. There are more opportunities for local companies to engage and participate in the semiconductor industry. We need to innovate, connect, and collaborate to strengthen the local semiconductor ecosystem.
There are stringent manufacturing requirements. There is focus on quality, quick turnaround times, having contamination-free work environment, etc. There are tool/process sensitivity and tight margins. We need to partner with fabs and other MNCs to understand the requirements to overcome the barrier to entry. As of now, GlobalFoundries is supported by Air Liquide Singapore, Kinetics Process Systems, Promech Services, etc.
GlobalFoundries does have experience with local SMEs. APEK is serving metrology tools. WF Industrialopolis is providing locally-produced consumable parts. We also have the opportunity for innovative robotics to improve labor productivity. Smart manufacturing is also helping us, provided by SixSense. We are using AI for automating defects classification replacing labor-intensive manual work. That is another advantage in quality. There are many other opportunities in building a strong and vibrant semiconductor ecosystem in Singapore.

Towards Industry 4.0
Ms. Jamie Neo, Director of Engineering, HP Inc., talked about the transformation journey towards Industry 4.0. HP has been present in Singapore since 1970. HP Singapore factory is among the 15 global firms joining the World Economic Forum’s leading-edge global lighthouse network.
In Singapore, HP started manufacturing since 1989. Efficiency is key! It is important for us to have efficiency and flexibility. We need to transform the way we do manufacturing. We are combining AI, industrial IoT, Big Data and analytics, robotics, and 3D printing. The smart factory is now a multi-year journey. We are digitizing the factory lines. We are doing cyber physical integration and embracing 3D.
HP SMARC, or smart manufacturing apps and research center, is the place to trial and prototype solutions. It looks at additive manufacturing, data analytics in manufacturing, robotics and automation, and industrial IoT. We are now using manufacturing apps. There is move, measure, check, record, and simplify.
We are now transforming to an intelligent factory. This will look at increasing the predictability and accuracy, reduce downtime, faster time to resolution, etc. We are also having a people strategy. HP is also navigating the change adoption cycle.